During our recent webinar, Cotton Dyeing: Technologies for a Sustainable Future, we received a number of insightful questions from our audience about sustainable dyeing processes and technologies. Our Cotton Incorporated experts Mary Ankeny, Vice President of Product Development & Implementation Operations and Buddy Garrett, Associate Director of Textile Chemistry Research, addressed these questions, providing valuable information and insights on the latest in sustainable dyeing.
What are the biggest barriers to the adoption of sustainable dyeing processes in the textile industry?
Mary – I think that people are going to say that cost is the biggest barrier. I feel like you need to really look at the cost. You can’t say “new dyes may be more efficient, but they’re more expensive.”
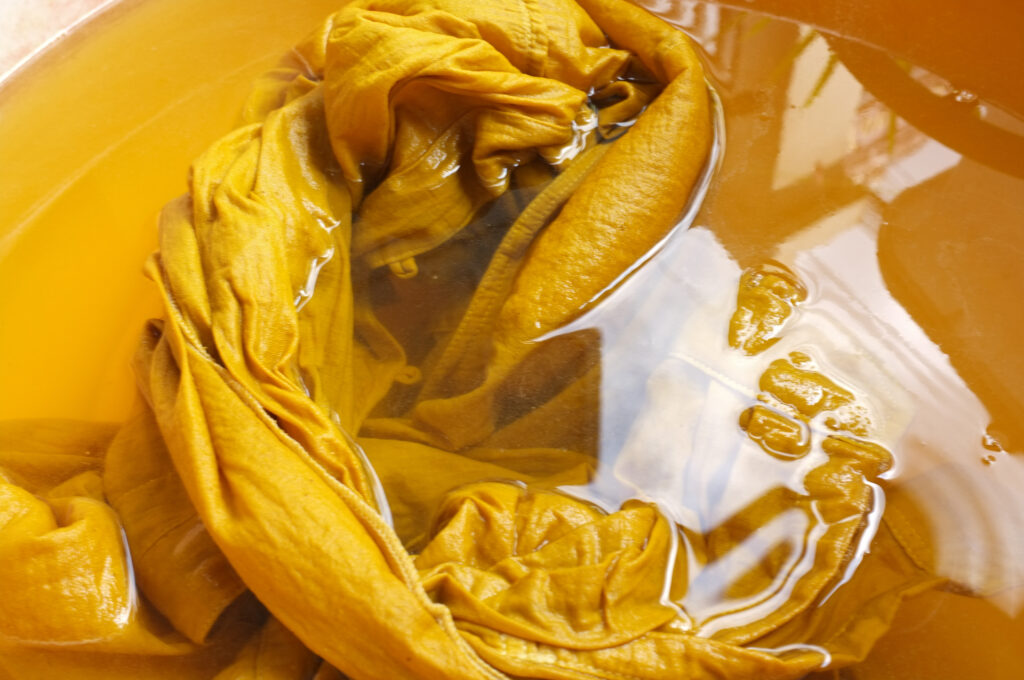
When you think about your whole process – can I use less of these dyes? Will these dyes enable me to use less energy? Will they enable me to wash more efficiently and use less water? You have to have a holistic view of your process, and likewise with equipment, once you’re able to understand how efficient your dye machine is or your dryer is, and you get a baseline understanding of what your costs are, then you may be able to justify the purchase of a new piece of equipment that will save you time, water, and energy.
That return on investment could make it very possible for you to upgrade your processes and enjoy some of the new technologies that are on the market.
How could someone communicate water and energy savings when the cost of the dye is higher than their current dye?
Buddy – One way to communicate water and energy savings is to use one of the measurement tools I mentioned earlier like One Way by Archroma® or Eliot by DyStar®. These tools, or ones like them, can help by capturing data on water consumption, electricity consumption, and steam consumption to use as comparisons between processes.
It is difficult to communicate water and energy savings if you are not currently measuring those metrics. The dye and chemical cost are usually the easiest part of the equation to measure, and one that is often looked at very closely by the dyehouse manager, so balancing that increased cost with water and energy cost savings can be difficult for dye suppliers to communicate. However, it can be done – and as the saying goes “what gets measured gets better.”
Is Zetaterra used for printing? Can it be used for rotary printing?
Buddy – Yes, it can be used for printing. We haven’t personally done that yet, but the mineral pigments can be used for printing. The best way to get information on using it for printing, including rotary printing, is to contact Zaitex in Italy for more information.
Can you explain how fabric can be dyed if there’s virtually no dye bath in the machine?
Mary – When we talk about dyeing cotton, we talk about dyeing at a 3:1 or 4:1 liquor ratio. And you can’t dye at 3:1 or 4:1 on just any dye machine. You really need to have a jet dye machine that is set up to be able to run the pumps at these low liquor ratios.
The dyeing takes place in the venturi. As long as you have enough dyebath liquor to uniformly wet the fabric and also enable the chemistry and dye solution to circulate through the pumps, you can utilize the lifter reel to aid the transport of the fabric to the venturi. In the case of the Then Airflow®, the fabric is moved through the machine by air. As long as you’re able to efficiently move that fabric through the venturi during the dye process, then you should be able to dye that fabric just fine.
How efficient is foam dyeing technology compared to traditional dye in terms of uniformity and depth of shade?
Buddy – With foam dyeing technology, fabric handling is going to be very important. We’ve done foam dyeing on a lot of woven fabric, because in our facility that’s how we have the fabric handled. In our application we found it works very well on a variety of shades, and one of the tricks that we use to get a nice uniform dye application is to divide the dye band over two different foam heads. That enables us to get a nice uniformity of the dye onto the fabric.
When it comes to performance of a foam dye – fabric performs just as well, we get good penetration into the fabric and we’re able to safely do a foam dye cure and get excellent dye fixation.
Are the high fixation dyes more expensive than the traditional reactive dyes?
Buddy – Yes, in most cases, the initial cost is more expensive, because there’s a lot of research that went into developing these dyes. A lot of the time, the chemical companies are trying to recoup that cost. However, you also have to look at it and measure it against the cost savings that we discussed earlier in terms of water, energy, and time savings that result from the higher efficiency high fixation dyes.
So you’re saving money on your rinses, you’re saving money on heating up water because you’re able to soap off at lower temperatures. And hopefully what happens over time is there’s volume increases in the sales and they become more competitive with traditional dyes. But you have to look at the whole picture.
Do you have any comments or insight on waterless dyeing technologies?
Mary – This is a new technology that has seen real gains for dyeing synthetic materials. One of the reasons is that it uses supercritical CO2 as the dyeing mechanism, and dispersed dyes are soluble in supercritical CO2. So you can dye polyester with dispersed dyes but you cannot dye cotton with dispersed dyes. So currently, waterless dyeing doesn’t really have an application for cotton dyeing.
How would someone reduce the washing cycles of reactive dyed cotton?
Buddy – One way is in using those higher fixation dyes that we talked about earlier. The higher the fixation you have, the more dye that’s covalently bonded to the cellulose fiber, the less dye you have to wash off. Also, if you’re able to use dyes that will require less salt and less alkali, those auxiliaries need to be washed out of that fabric.
So in order to reduce the number of washes, you want to be able to use less dye, less salt, and less alkali – so that you’re able to rinse faster.
Also, the machinery has a lot to do with it. How well does the machinery displace that water that contains that loose color into it as well? So in order to reduce that, you’re looking at methods that will remove as much color, get it away from that fabric and down the drain, and have less color in the first place by using dyes that have a higher fixation rate.
Any insight on print technology?
Buddy – In terms of print, there is digital print technology, but that within itself could be an entirely separate webinar. But there is quite a bit of technology in terms of digital printing. A lot of the time, that’s with patterns as well.
When we talk about printing cotton, typically cotton can be printed with pigments or dyes and digital printing has been growing over the last 20 years and is available to print on cotton with pigments and reactive dyes, and also is developed to print on other fabrics as well, using pigments and dispersed dyes or acid dyes.
The benefits of digital printing are that you don’t have to make a screen. The amount of waste generated by digital printing is also extremely low. Traditionally, if you’re printing cotton with reactive dyes, you would pretreat your cotton fabric with alkali or an anti-migrant, and then you can print on the fabric directly with the dyestuff.
You can print not only in full width, you can also print pattern pieces so that you can take it right to the cutting machine and cut those pieces out. And there’s also direct to garment printing, which replaces the need for screen printing.
I think there’s a lot to be said about the different types of printing technologies that are out there, but it’s absolutely a sustainable approach to printing.
How available are these technologies in different parts of the world?
Buddy – All of the technologies we’ve talked about in this webinar are readily available. They’re located in different locations, whether it’s in Europe, North America, Asia…the origin of these technologies is all around the world, and they’re available all over the world.
As Cotton Incorporated, we’re a global company with a global outreach, so in that regard, we’ve talked about things that are available globally.
A lot of the chemical companies we’ve discussed can be sourced globally, as well as the machinery companies. It’s just a matter of making those contacts with these companies.
What is the performance level of the EarthColors® dyes?
Mary – The performance of the earth color dyes is going to match the performance of traditional sulfur dyes. So these are the Archroma EarthColors® that are biosynthetic. You’re replacing some of the petroleum based components of these dyes with natural materials, but the performance is equal to what you would see through their Diresul® dye range.
The product also replaces petroleum with cotton byproducts, so you’re dyeing cotton with cotton.
Are Recycrom dyes applicable for exhaust dyeing?
Buddy – Yes, the Recycrom dyes can be exhaust dyed.
If significantly less salt is added, how is repulsion reduced without using any cationic finish?
Buddy – Salt is needed in traditional dyebaths to drive the dye from the dye bath to the cellulosic fiber, since both the dyestuff and the cotton substrate are carrying a negative charge. As mentioned, in a high liquor ratio dyebath, a cationic charged cotton substrate would alleviate these repulsive charges and allow the cationic charge on the cotton to attract the negatively charged reactive dyestuff.
However, in the extremely low liquor ratio dyeing scenarios described in the presentation, the dyestuff is inherently in contact with the cotton fabric through absorption and the need to “drive” the dye out of the bath and onto the substrate using salt is drastically reduced. In the case of reactive dyeing, with the extremely low liquor ratios of 1:1 or less, the dyestuff is already in close enough proximity that the dyestuff will covalently bond to the cellulosic fiber when placed under alkaline conditions without the need for traditional levels of electrolytes. With no additional dyebath that is not in contact with the fabric, the dyestuff has nowhere else to go despite the repulsive forces of the negatively charged dyestuff and the negatively charged fiber.
The journey towards more sustainable practices in the textile industry is ongoing, and your engagement and questions are crucial in driving this progress. For more information on this topic, visit the CottonWorks™ dyeing section.