Product Innovations for Creating with Cotton
The textile industry is constantly evolving, and cotton remains at the forefront of innovation and design. With CottonWorks™, you can stay ahead by accessing free digital fabrics, the Material Library, and the Trend Forecast to support your design and development process.
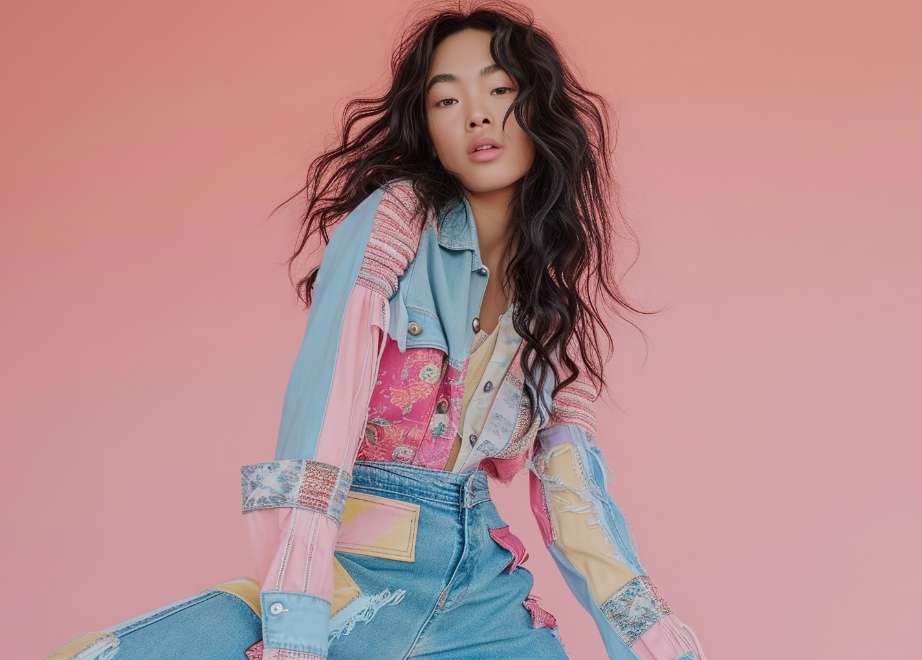
Cotton Material Library
The Material Library streamlines product development by putting seasonally updated fabrics at your fingertips to inspire your design and development. Cotton Incorporated’s FABRICAST™ library exhibits a wide range of cotton-rich fabric collections, from knits to denim and beyond.
Digital Product Creation
CottonWorks™ members can download free, high-quality fabrics that are ready for 3D clothing design software. Compatible with both CLO3D and Browzwear, these digital fabrics are frequently updated to reflect the industry’s latest trends and designs.